Learn How We Make Our Metal Beds

We’re proud of our hard-earned reputation for producing top quality hand cast iron, brass and nickel bed frames which are designed and built to last a lifetime.
It’s as far from a production line as you could get.Our small team of committed artisans are still using the same techniques championed by their Victorian forefathers, and the time and skill they invest is evident in the end result.
Visitors to our foundry at Par in mid-Cornwall can see first hand the entire manufacturing process. Our iron beds have a modest birth, starting out as lengths of seamless tube which are cut to size and then crimped at either end.

The tubes, which will form the vertical features of the bedsteads, are then laid across a base set of moulds (these vary depending on the design chosen by the customer) and topped. An engineer with a very steady hand uses a ladle to spoon molten zinc, which reaches temperatures of 470ºC,from the nearby furnace and pour it into the moulds' cavities.

As it cools, the zinc solidifies and is then knocked free. Any spigots are removed and recycled. At this stage, a unique cast knuckle joint is used to attach the side rails to the foot and head of the bed.

Our signature self-locking system guarantees longevity, and is incomparable to modern, flat pack beds which are often held together with flimsy bolts.
What started out as incongruous tubes of metal is now taking shape. Any remaining flashing is cleared and the frame is hand-fettled using angle and die grinders to remove any imperfections.

An individual serial number is stamped on the knuckle, making it bespoke for each customer, and centre supports are installed, depending on the size of the bed.

The frame is then de-greased by hand before powder coating is applied using an electrostatic gun, and cured in an oven at temperatures reaching 400ºC. The baked ‘skin of paint’ is thicker and more durable than its conventional counterpart and extremely unlikely to chip. We offer nine standard colour options, but are happy, for a small cost, to source paint of any hue requested by our customers.
Now nearing completion, we attach brass accessories which are then lacquered and left to dry.

Quality control is maintained throughout the manufacturing process and, after one final check, the finished bed is wrapped ready for delivery. Each bed has a certificate of authenticity attached to its head. All deliveries include assembly in the customer’s home, and we take away all the packaging.
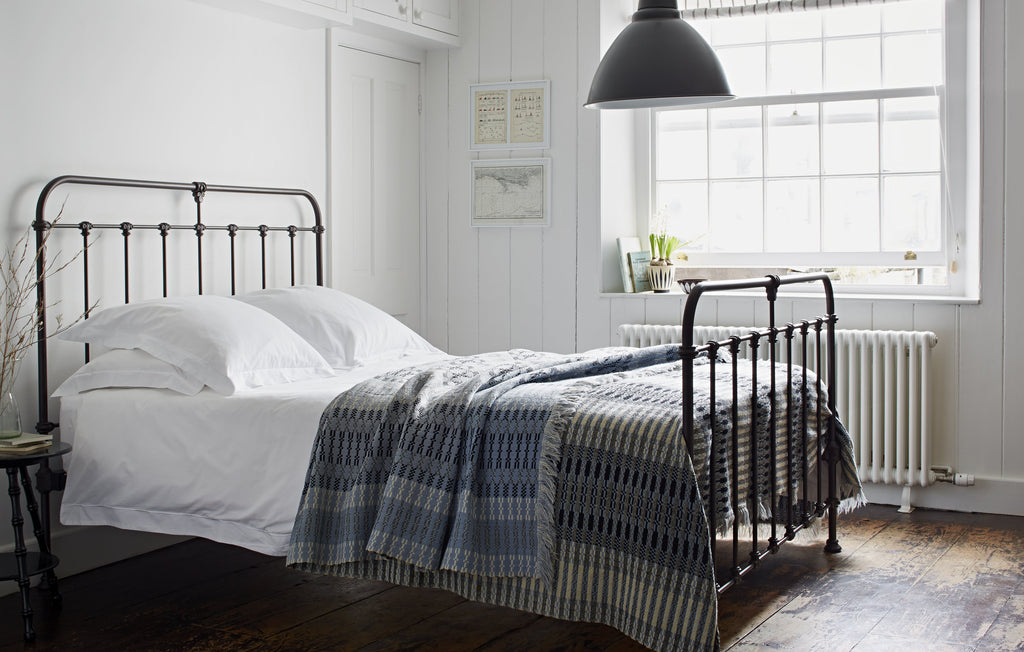
We’re confident that we produce some of the finest beds found anywhere in the world - and are proud that we do from our base in the heart of Cornwall.